ABQ FTZ Case Studies
Examples of How an FTZ Can Be Used
Typical Industries that Use FTZs
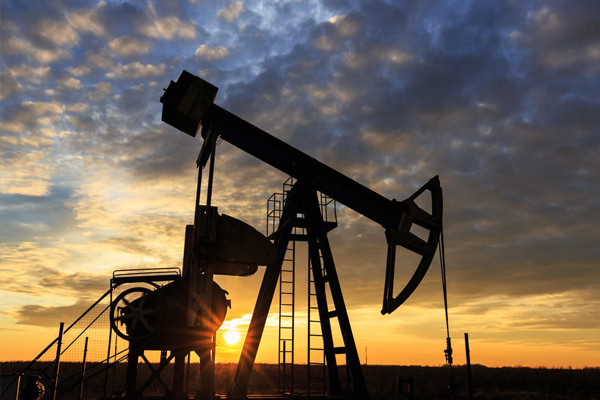
Oil & Gas
The petroleum industry, also known as the oil industry or the oil patch, includes the global processes of exploration, extraction, refining, transporting (often by oil tankers and pipelines), and marketing of petroleum products. The largest volume products of the industry are fuel oil and gasoline (petrol).
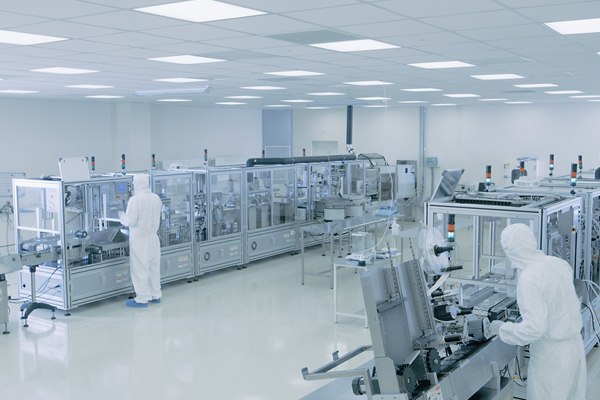
Intelligent Manufacturing
A report released by Ernst & Young, ranked New Mexico 1st in the west for manufacturers with the lowest effective tax rate for manufacturing. New Mexico is home to 3 national research facilities and 3 nationally-recognized research universities. The state is ranked 1st in non-industry investment in research and development and 9th in high-tech jobs.
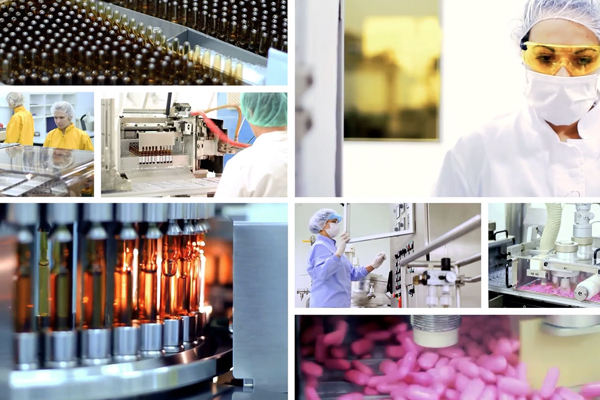
Pharmaceutical
By operating in an FTZ, drug makers can avoid duties on raw materials and APIs, and elect to pay the lower or zero duty when finished drug products leave the zone for sale in U.S. commerce. Operating within an FTZ also allows pharmaceutical companies to reduce cycle time through direct delivery.
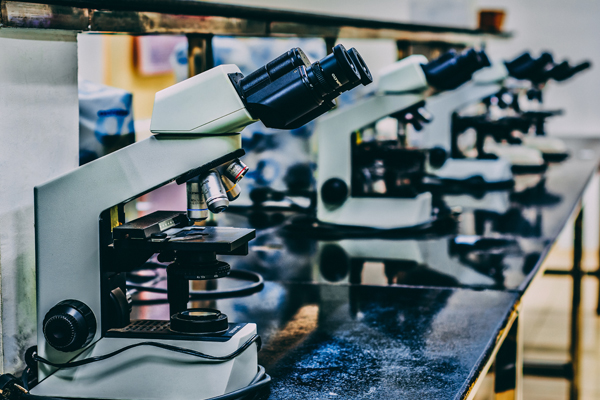
Research & Development
Research and development capacity, combined with plentiful natural resources, an excellent climate, low cost of doing business and aggressive job creation incentives equate to a growing manufacturing sector when other states are experiencing declines. The New Mexico Small Business Assistance Program allows a business to use a scientist, engineer, or facility to test a product or develop a prototype. Intel, Honeywell, General Mills, Johnson & Johnson, and Tempur-Pedic all have manufacturing facilities in New Mexico.
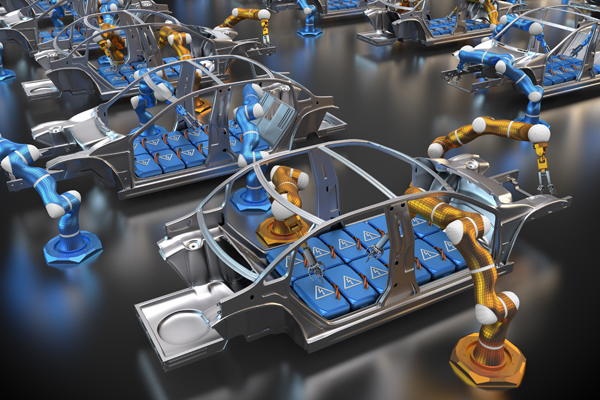
Auto Technology & Manufacturing
Fuel Cells and Batteries. Manufacturing vehicles in a foreign- trade zone is the same as manufacturing vehicles anywhere– but with some
very distinct advantages. If a shipment arrives at midnight and is needed on the assembly line, that shipment can be received into the inventory control system, taken straight to the line for use, and then be reported to Customs and Border Protection the next day. The cost of a line-down situation far exceeds any duty savings to be realized.
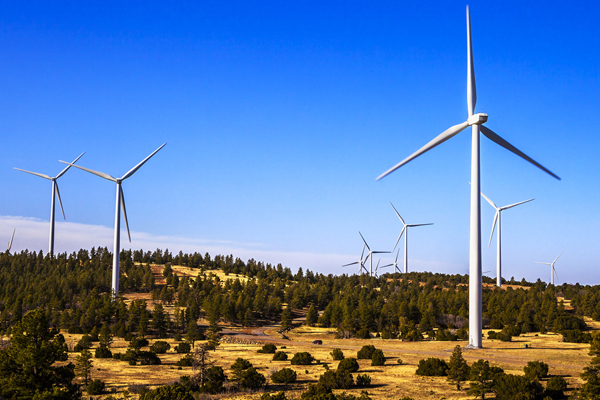
Alternative Energies
New Mexico has plentiful natural resources and is the eighth-largest energy producer in the nation. About 50 percent of the electricity generated here is exported. All of the state’s new and planned electricity generating capacity will use renewable energy or natural gas.
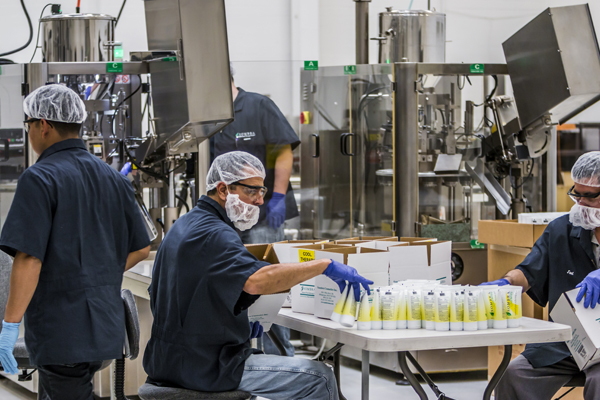
Consumer Products
In New Mexico, intelligent manufacturing often begins with a new technology born here. Companies like SolAero, UbiQD and 3D Glass Solutions are all examples of companies manufacturing products with a commercialized New Mexico technology. Great incentives like JTIP and LEDA, and the West’s best climate for manufacturing are all great reasons to make your product here. New Mexico companies manufactures a variety of consumenr related products from microprocessor technology to herbal dietary supplementsto metal fabrication for appliances, to tissue, towels, napkins and dispensers.
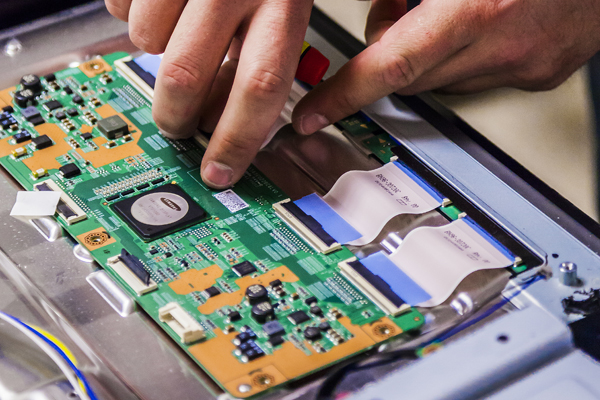
Final Assembly Products
A product that includes foreign components may be called “Assembled in USA” without qualification when its principal assembly takes place in the U.S. and the assembly is substantial. For the “assembly” claim to be valid, the product’s last “substantial transformation” also should have occurred in the U.S.
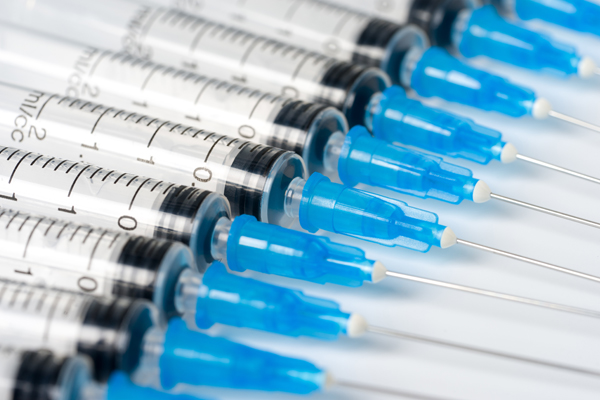
BioMedical
New Mexico Consortium (NMC) researchers study microbiology, immunology, structural biology, bioinformatics, genome research and modeling. This combination of capabilities along with the cutting-edge NMC research facilities enables our scientists to carry out forefront basic research on the role of immune systems in countering major pathogen threats.
Foreign Trade Zone Savings Examples
Cash Flow Savings/FTZ Borrowings Reduction Savings Example
Imported merchandise is stored before being utilized and/or distributed to their ultimate destination in the U.S. or overseas. While the inventory generally may move very quickly, the average value of on-hand inventory subject to U.S. Customs duties is significant. The postponement of Customs duty payments on the imported merchandise will result in cash flow savings to the Company. In the past, companies used to take this amount and multiply it by a borrowing rate factor. We have labeled this savings category “FTZ Interest Savings.” Alternately, many companies now count the cash outlay on Customs duties paid to support the average on-hand inventory as a reduction in borrowings. We have labeled this optional savings category as “FTZ Borrowing Reduction Savings.” The average on-hand inventory value of $25,000,000 has a value for Customs duty of $1,500,000 ($25,000,000 x 6% Customs duty rate). This is the “FTZ Borrowing Reduction Savings.” A conservative approach is to multiply $1,500,000 by a suggested interest rate (5%) which equals $75,000. This is the “FTZ Interest Savings.” Either of these methods may be utilized to calculate the Company savings on cash flow. We have broken out the savings with both methods. This will provide two total financial savings totals at the end of the worksheet. These totals are identical except that one includes the “FTZ Borrowing Reduction Savings” calculation and the other includes the “FTZ Interest Savings” calculation for the cash flow category.
Inverted Duty Savings Example
Imported parts may be subject to duty rates that are higher than the finished product. Generally, production is determined when the Harmonized Tariff Schedule of the United States (HTSUS) classification number on the imported parts/material changes to a different number during production or processing. The average Customs duty rate of 6% would normally apply to the imported parts/materials without a zone. The materials are admitted to the zone and produced/kitted into a finished product with a 0% Customs duty rate. Utilization of foreign-trade zone procedures will allow the Company to choose the Customs duty rate of the finished product (0% versus 6%) rather than the Customs duty rate that normally applies to imported parts/materials. This places the U.S. production facility in the same financial position with regard to U.S. Customs duties as foreign production facilities. This may be the most important area for financial savings. The imported parts/material value ($100,000,000) would normally have a 6% Customs duty rate or a Customs duty value of $6,000,000. However, by choosing the Customs duty rate that applies to the finished product (0%), the duty value will decrease to $0.
Merchandise Processing Fee/Customs Broker Entry Fee Example
Imported parts may be subject to duty rates that are higher than the finished product. Generally, production is determined when the Harmonized Tariff Schedule of the United States (HTSUS) classification number on the imported parts/material changes to a different number during production or processing. The average Customs duty rate of 6% would normally apply to the imported parts/materials without a zone. The materials are admitted to the zone and produced/kitted into a finished product with a 0% Customs duty rate. Utilization of foreign-trade zone procedures will allow the Company to choose the Customs duty rate of the finished product (0% versus 6%) rather than the Customs duty rate that normally applies to imported parts/materials. This places the U.S. production facility in the same financial position with regard to U.S. Customs duties as foreign production facilities. This may be the most important area for financial savings. The imported parts/material value ($100,000,000) would normally have a 6% Customs duty rate or a Customs duty value of $6,000,000. However, by choosing the Customs duty rate that applies to the finished product (0%), the duty value will decrease to $0.
Harbor Maintenance Fees Example
A Harbor Maintenance Fee is assessed at the rate of .125% on the value of all ocean freight imports. In an FTZ, instead of paying the fee at the time of Customs entry filing, it is paid quarterly on a CBP Form 349/350. The cash flow savings should be considered.
Inventory Tax/Other Taxes Example
Section 81o(e) of the FTZ Act provides for an exemption for foreign merchandise admitted to a zone and domestic merchandise held for export. There are also other types of tax savings in certain states specifically for activated foreign-trade zones. The tax mechanism for any exemption is different in each local jurisdiction.
Scrap/Waste/Obsolete/Surplus Losses Example
A certain percentage of annual imported merchandise become scrap, waste, or obsolete during receiving, production, processing, storing, or merchandise shipping. With proper accounting procedures, zone status enables companies to avoid Customs duties on such merchandise. For example, the initial product to be produced in the zone could have a 3% waste factor. The value of the imported merchandise for this period is $100,000,000. This number multiplied by the 3% waste factor equals $3,000,000 as the value of merchandise that is identified as scrap/waste during production. The 6% Customs duty on this merchandise if paid would total $180,000. Payment can be avoided through production under Zone procedures. If merchandise is sent to a landfill/incinerated, the value is zero. However, recycling of this merchandise creates a new value that may or may not have a rate of duty. This is an area that should be further discussed.
Zone-to-Zone Transfers Example
Merchandise admitted to the zone can be transferred in bond to another zone or subzone without a Customs entry. Zone status would allow customers of your facility to ship product to other zone locations that store or produce finished products at a considerable savings. This is a difficult area to quantify in dollars, but is worth identifying as it can attract the business of other companies located in zones. It may provide a benefit for suppliers or customers that are located in zones.
Exports Example
A company can generate significant financial savings by avoiding Customs duty payments, merchandise processing fees, and the significant expense and complexity of duty drawback on all exported products. The Customs duty drawback program recovers duties paid on imported finished products that are subsequently re-exported. However, full financial recovery is never achieved for a variety of reasons. The U.S. Customs duty drawback procedures are complex, expensive, and not time sensitive.
Further, if your organization has finished products in the future that are subject to antidumping or countervailing duties or Section 232 Chapter 99 duties, the zone is another opportunity for financial savings as Drawback is not available for these three types of additional duties. Zone procedures provide savings by never paying the special antidumping or countervailing Customs duties or the Section 232 Chapter 99 duties. Initially, if 20% of the finished product that will be produced in the proposed zone is exported, a significant savings is achieved. This represents a value of $20,000,000 ($100,000,000 annual import value x 20% exported). Under the example provided in the worksheet, the Customs duties that will be avoided through use of the zone is 2% ($20,000,000 x 2%). This amount of duty would have to be paid in an identical transaction without a zone.